PLC's are the building block of our modern industrial environment. Without them accident (error) prone manual labour would prevent us from being competitive in our modern free world. They have a multitude of uses apart from controlling machinery, eg:. Data logging for quality control records, inexpensive but sophisticated time clocks, temperature and environmental controllers are to name but a few.
  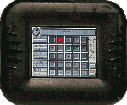
Ceeps works with the Koyo brand of PLC's. These Direct Logic PLC's range from fixed I/O units to modular systems with thousands of I/O, used for simple machine sequencing to process control.
Ceeps design and build custom made electrical control panels to carry out specific tasks such as, controlling the automated process in a production line, controlling cut to length machinery and controlling temperatures in cold stores and blast freezers. PLC's are also used for data logging purposes and time dependent processes.
|